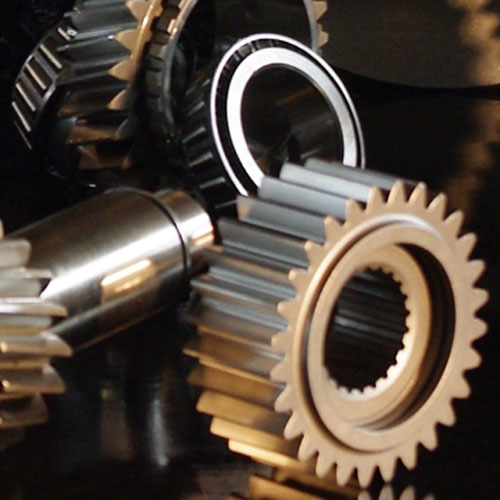
The trip took place just on the anniversary of the manufacturer - this year CEI turns 50 years since its foundation. Therefore, it was doubly interesting for guests to see how the company works with such a long tradition, how the production process is improved and high quality standards are maintained.
The guests visited the huge CEI industrial site located near Bologna, in the Emilia Romagna region. The factory complex includes production department, as well as a design, engineering departments, its own laboratory, a tool department and packing line.
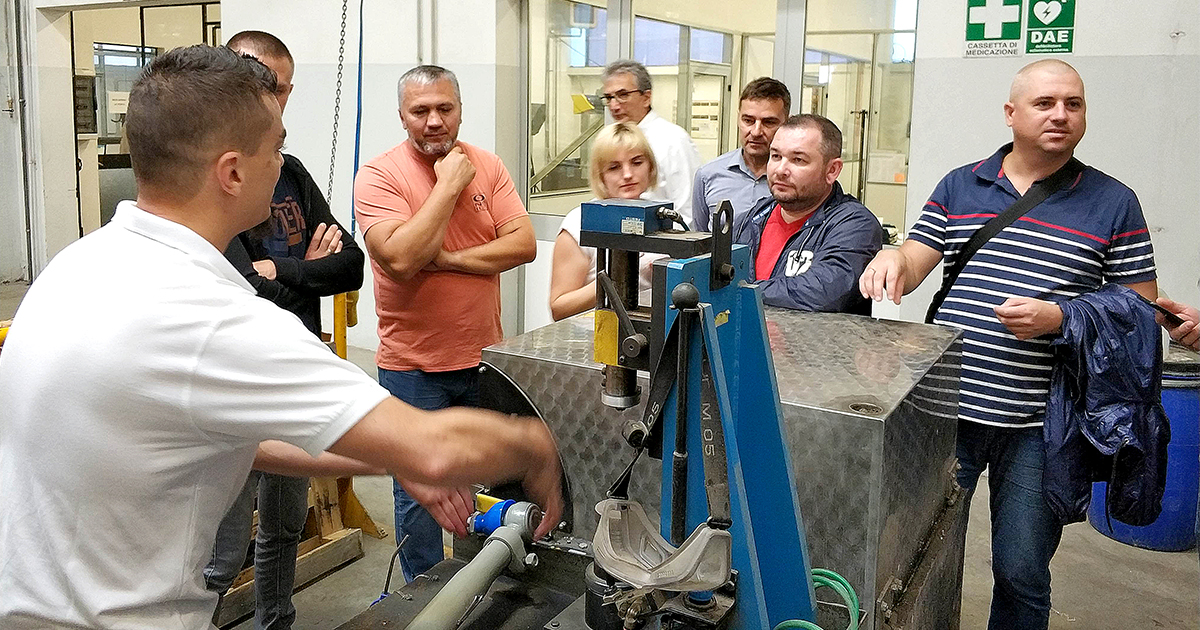
Checking the SCANIA steering rod on the mount for compliance with European standards
Laboratory has a great importance in the work of the plant. There is equipment for product quality control here. Tests are performed not only at the output, but also at each production stage. Products undergo a five-step test, due to which the scrap level is kept at the point of 0.5 - 0.7%. At the same time, off-spec products never hit the market.
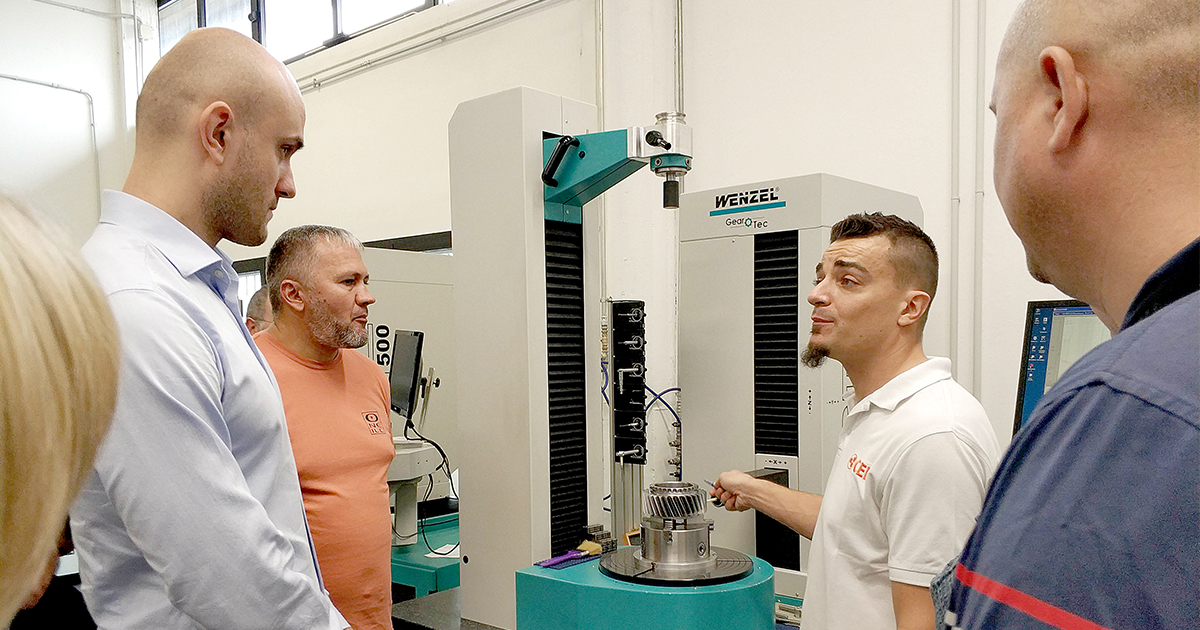
Demonstration of the split-second indicator of the internal surfaces of the components
There are installed 3D lasers in the laboratory, in the components modeling department that can scan the components with high accuracy and display it in exquisite detail on the monitor. Even for components with complex geometry, obtaining an accurate 3D model using a laser is not a problem. Also the mounts stand in the laboratory to tests components on loading, rupturing of the material and other indicators. For example, the thickness of the molybdenum deposition layer on the gear is checked on the equipment, and it is tested for hardness and softness. Thanks to such thorough checks, the quality of the products complies with the requirements recommended in the European Union.
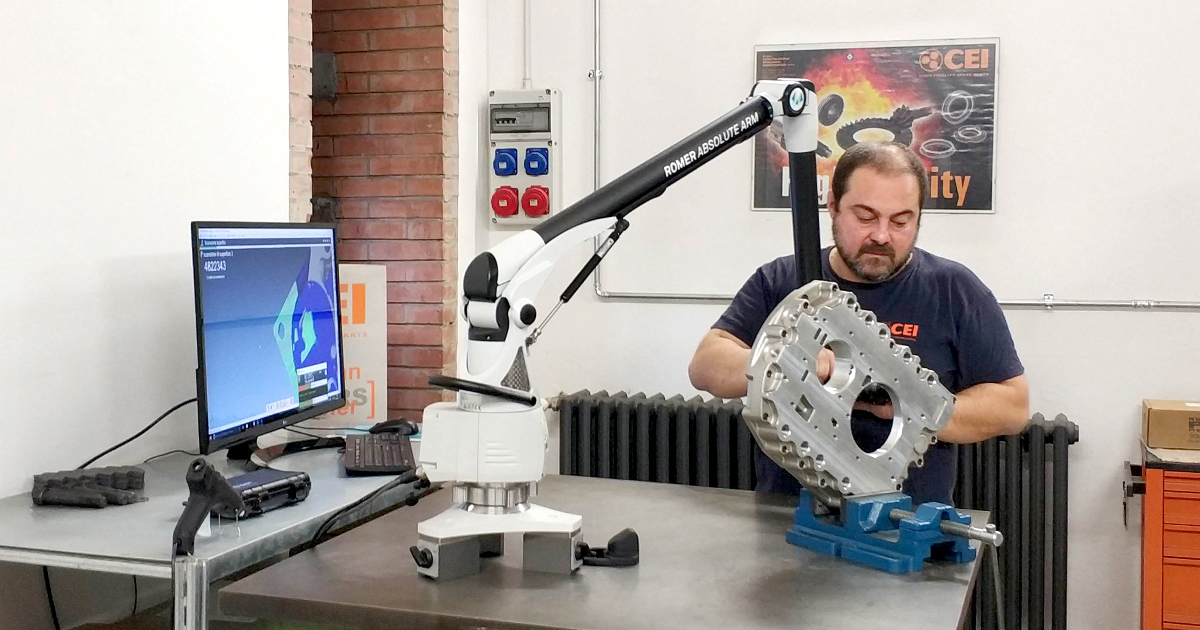
A 3D laser scanner that scans geometry-complex parts and creates a 3D model on a computer
Almost all lines at the plant are automated and form a closed production cycle. About 40 machines operate here - mainly the German brand LIEBHERR, as well as American and Italian manufacturers. In addition, CEI takes care of the environment, so metal waste is recycled and reused.
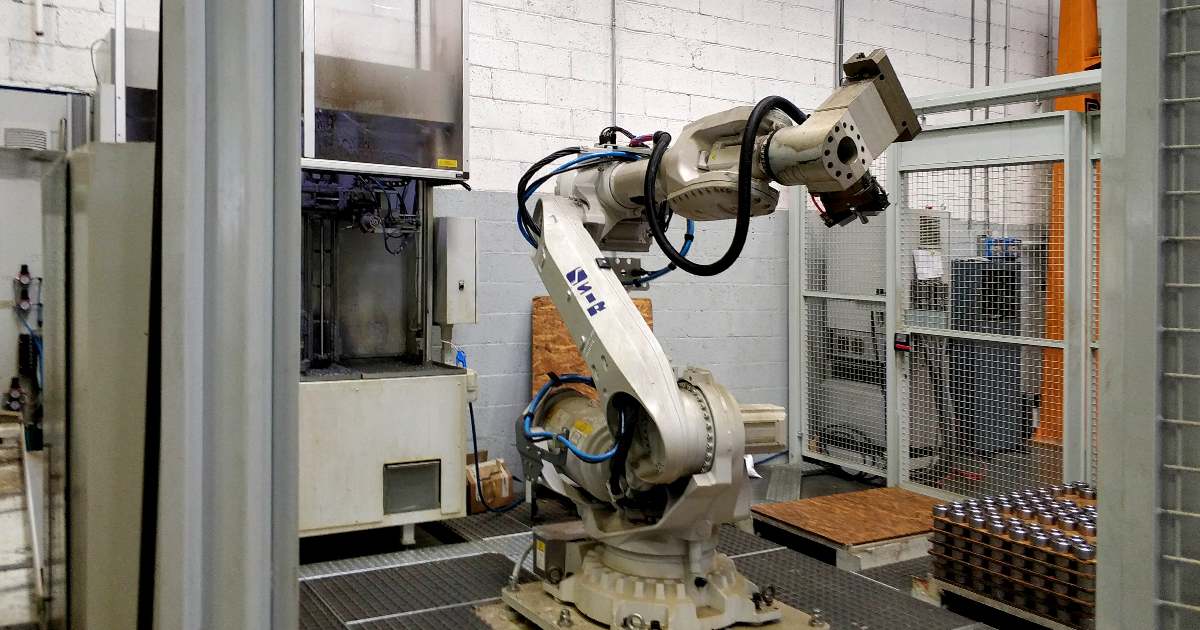
Robotic arm
In production, only high-quality materials are used that are not inferior to the original and are additionally checked in the laboratory for compliance with the requirements. Components are selected from world manufacturers: premium segment bearings from FAG, INA and SKF and the mid-segment from Fersa.
The plant produces components not only for the after-market, but also genuine spare parts. The manufacturer delivers traction to the BPW line, flywheels to the New Holland plant, and gears to the IVECO line. The company annually produces more than 500 new products, and 1,500,000 stock-keeping units for trucks and buses are constantly in warehouse.
During the three days trip, the guests not only studied the production process, but also went on excursions to Florence and Bologna, which gave a lot of vivid emotions and unforgettable impressions.
We thank CEI for an interesting trip and a warm welcome.